Injection Molding
What is Injection Molding?
Injection molding is a manufacturing process used to produce parts by injecting molten material into a mold, where it cools and solidifies into the desired shape.
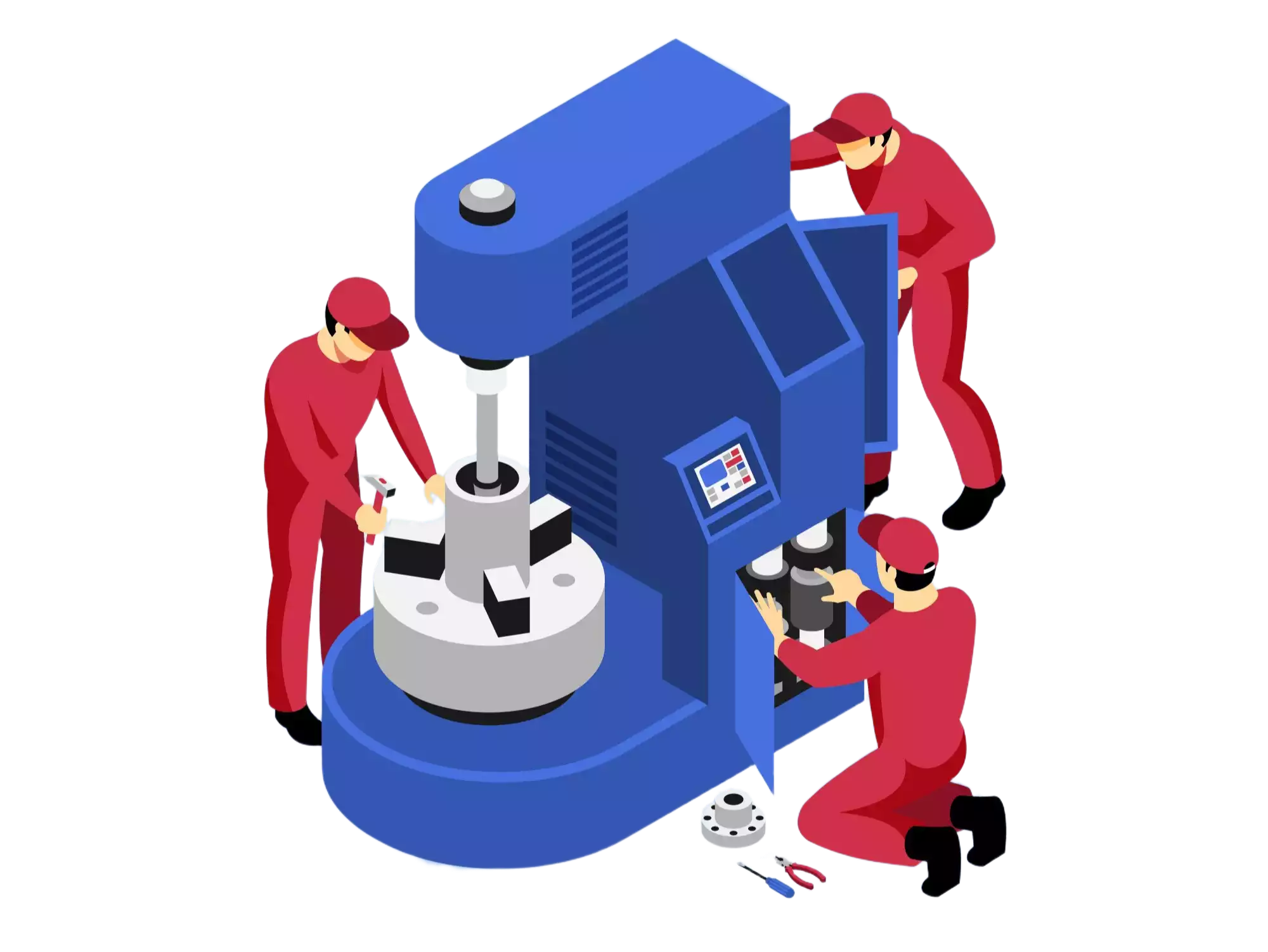
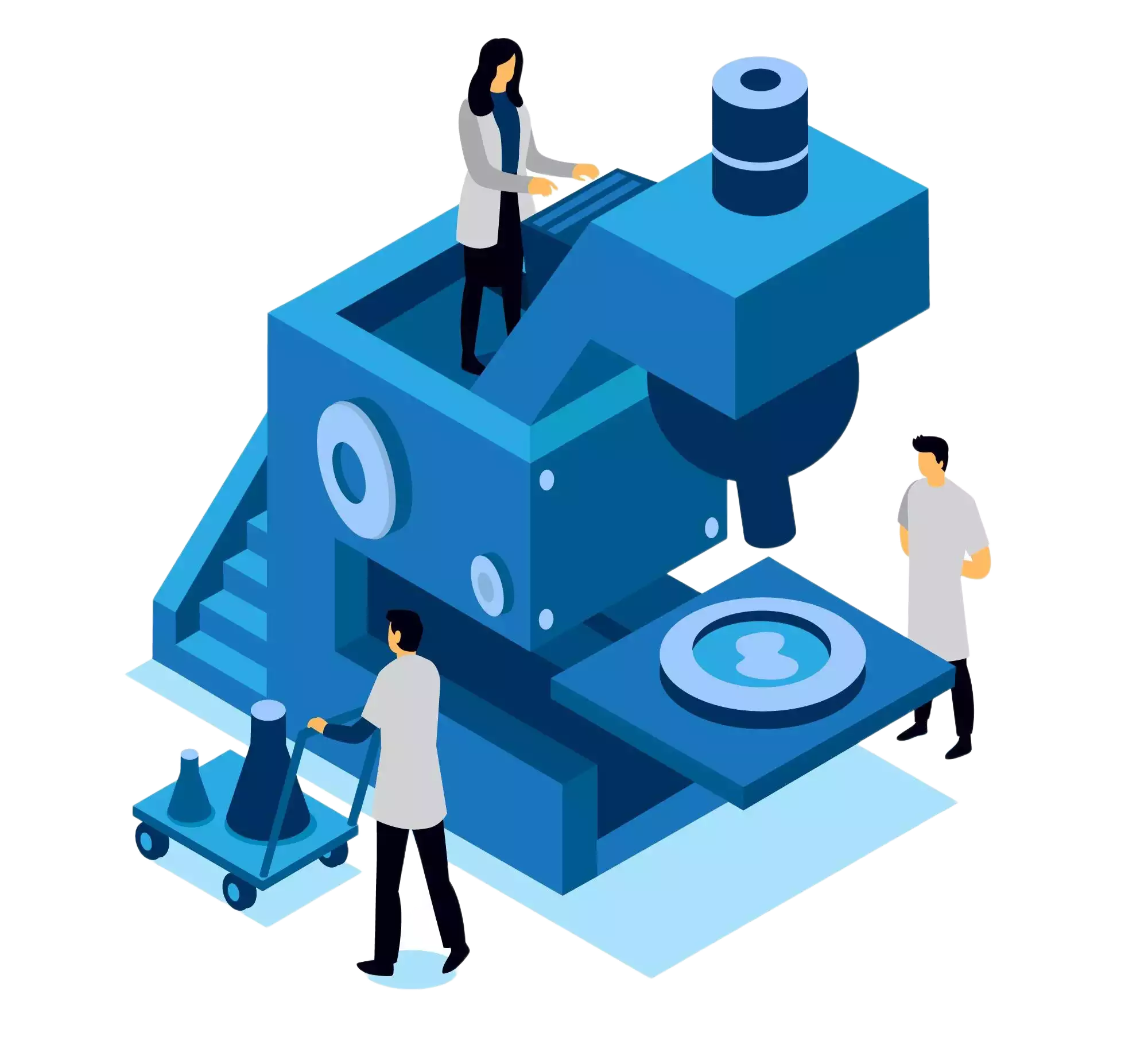
Key Features
High Production Efficiency
Once molds are developed, the process is extremely fast with cycle times as short as 10 seconds, making it ideal for medium and high-volume production runs.
Low Cost per Part
For high output production runs, the cost per part is very low. Even for medium volumes, costs can be kept down by using aluminum molds instead of steel.
Repeatability
Identical products can be manufactured repeatedly, ensuring high tolerances and reliability across high volumes.
Large Material Choice
A wide range of plastic materials can be selected depending on the desired properties of the final part.
Minimal Post-Processing
Parts usually have good aesthetics post-production, requiring little or no additional processing.
How Does Injection Molding Work?
Injection molding involves melting plastic materials and injecting them under high pressure into a mold cavity. The molten plastic cools and solidifies, taking the shape of the mold.
Types of Injection Molding
- Thermoplastic Injection Molding: Uses thermoplastic materials that can be melted and solidified multiple times.
- Thermoset Injection Molding: Uses thermosetting materials that undergo a chemical change when heated, solidifying permanently.
- Liquid Silicone Rubber (LSR) Injection Molding: Involves injecting liquid silicone rubber into a mold, suitable for parts requiring high-temperature resistance and flexibility.
Materials Used in Injection Molding
- Thermoplastics: Materials like polyethylene, polypropylene, and polystyrene that can be melted and solidified multiple times.
- Thermosets: Materials like epoxy and phenolic that undergo a chemical change when heated, solidifying permanently.
- Elastomers: Materials like rubber that offer flexibility and resilience.
Advantages of Injection Molding
- High Production Efficiency: Fast cycle times make it ideal for large production runs.
- Low Cost per Part: Economical for high-volume production.
- Repeatability: Ensures consistent quality across large quantities.
- Design Flexibility: Allows for complex shapes and integration of multiple features into a single part.
- Minimal Post-Processing: Parts often require little to no additional processing.
Applications of Injection Molding
- Automotive Industry: Production of interior and exterior parts.
- Consumer Goods: Manufacture of items like toys, containers, and household appliances.
- Medical Devices: Creation of components requiring high precision and biocompatibility.
- Electronics: Production of housings and components for electronic devices.
The Future of Injection Molding
The future of injection molding includes advancements in materials science, such as the development of biodegradable plastics and composites, as well as improvements in automation and integration with additive manufacturing technologies.
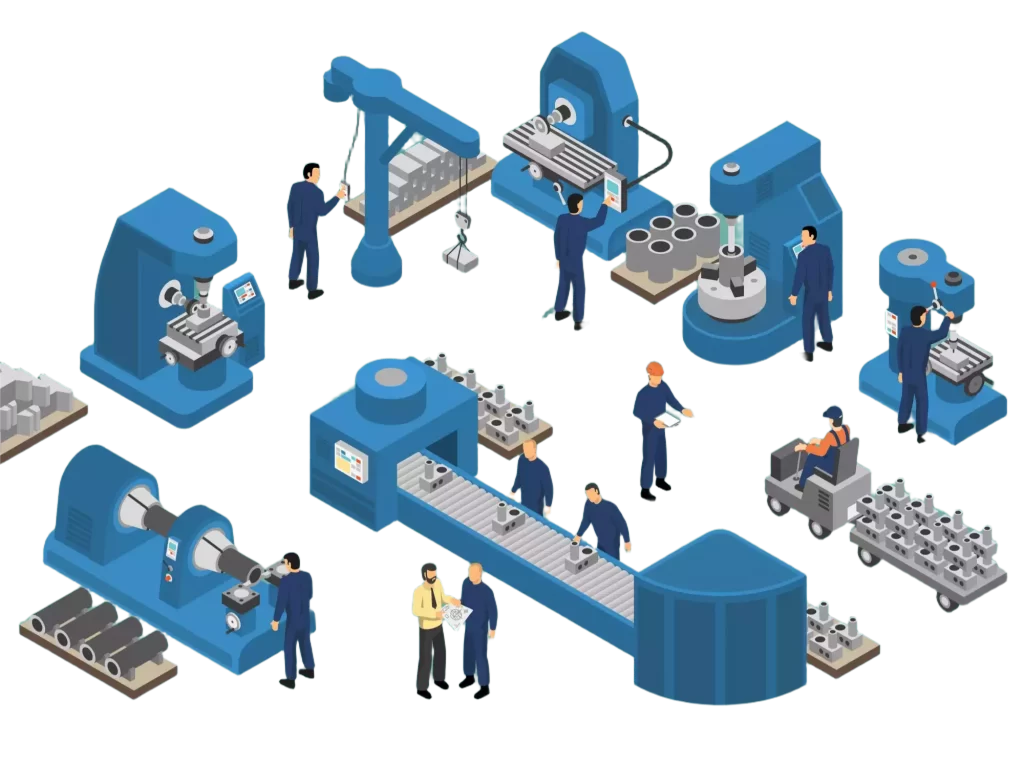
7 Tips for Choosing an Injection Molding Service
Experience and Expertise
- Select a provider with a proven track record in your industry.
Quality Assurance
- Ensure they have robust quality control processes in place.
Material Selection
- Verify they offer a wide range of materials suitable for your product requirements.
Production Capabilities
- Assess their ability to handle your production volume and timelines.
Design Support
- Check if they provide design assistance to optimize manufacturability.
Cost Competitiveness
- Compare pricing to ensure it aligns with your budget.
Customer Service
- Evaluate their responsiveness and willingness to collaborate.
Choosing the right injection molding service is crucial for the success of your project, ensuring quality, efficiency, and cost-effectiveness.
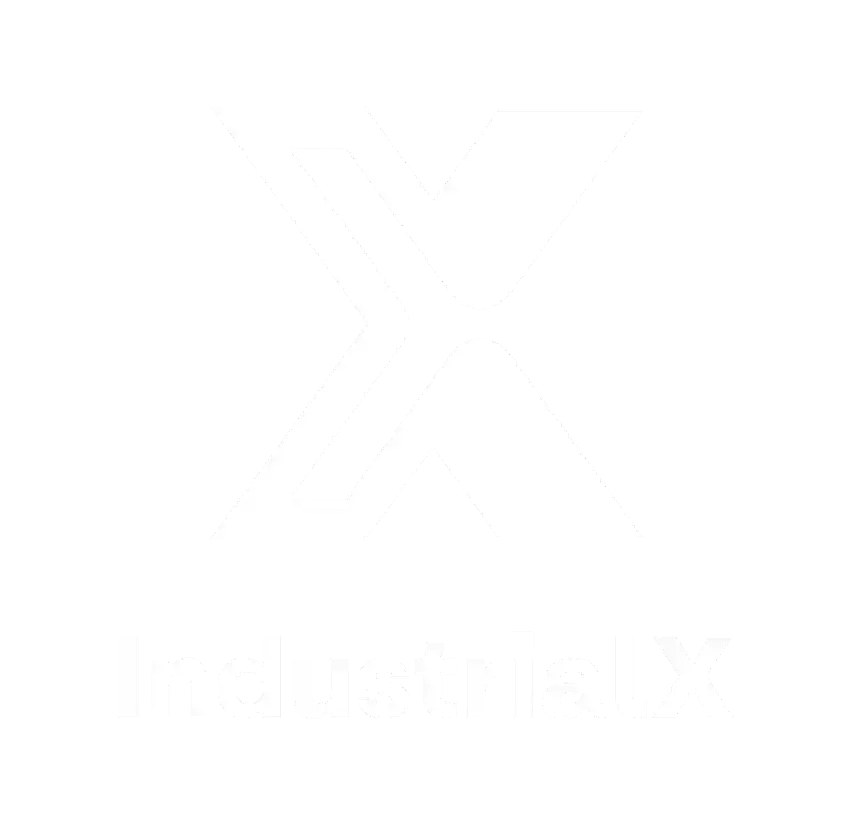
We connect buyers with trusted suppliers to ensure you get the right products for your business needs.
IndustrialX is the ultimate one-stop marketplace for businesses in the automotive and industrial sectors, providing a seamless way to find, compare, and purchase high-quality industrial equipment.
Manufacturing Services
Manufacturing Capabilities to Meet Your Needs
Customer base
manufacturers
CNC Machining
A precise manufacturing process using computerized machines to cut, shape, and finish materials with high accuracy.
Read more3D Printing
A process that creates three-dimensional objects layer by layer from digital models, enabling rapid prototyping and customization.
Read moreSheet Metal
The process of shaping metal sheets into desired forms using cutting, bending, and stamping techniques.
Read moreInjection Molding
A manufacturing process where molten material is injected into a mold to create parts with high precision and detail.
Read moreDie Casting
A process where molten metal is forced into a mold to create durable and complex parts with precise detail.
Read moreAssembly Products
The process of putting together different components to create a finished product, ensuring functionality and quality.
Read more